سنگ آهن در زمین ابتدا شناسایی شده و سپس حفاری جهت استخراج صورت میگیرد پس از انفجار تبدیل سنگ به قطعات قابل حمل سنگ آهن به کارخانه هایی فرآوری هدایت میشود. در مرحله اول فرآوری سنگ آهن، پیش از ریختن مواد در سنگ شکن، قطعات کوچک توسط سرند جدا میشوند. این کار، وزن خوراک سنگ شکن در مرحله بعدی را کاهش داده و باعث افزایش بهرهوری میشود. وجود قطعات ریز انرژی مصرفی را افزایش میدهد. به همین دلیل، فرآیند سرند کردن از اهمیت بالایی برخوردار است. سرندهای ارتعاشی یکی از پرکابردترین تجهیزات مورد استفاده در این مرحله هستند.

مراحل سنگ شکنی سنگ آهن
پس از سرند کردن مواد معدنی، ذرات بزرگ به بخش سنگ شکن انتقال داده میشوند. هدف از خردایش و رساندن ابعاد سنگ به اندازه های کوچکتر و، بهبود فرآیند فرآوری و کاهش هدررفت زمان در مراحل بعدی است. این بخش اولین بوده و جز پرهزینه ترین قسمت های کار گاه به حساب میآید.
به طور کلی بیش از نیمی از هزینه فرآوری و بیش از 70 درصد انرژی مصرفی در کارگاه مربوط به این قسمت است، در نتیجه بررسی و کاربرد روش هایی که بتواند در کاهش مصرف انرژی و هزینه تاثیر گذار باشد، میتواند در اقتصاد کارگاه نقش مهمی را ایفا کند. برای خرد کردن از سنگ شکن های متفاوتی می توان استفاده کرد. معمولا سنگشکنهای فکی، ژیراتوری و مخروطی مورد استفاده قرار میگیرند. حال که محصولی با ابعاد کمتر از ۳۰ میلیمتر به دست آمد، باید آن را وارد مرحله آسیا کنی نمایند که این مرحله با حضور آب و به صورت تر انجام میگیرد.

برای بررسی قیمت و خرید پوسته اکسیدی آهن وارد لینک روبرو شوید – پوسته اکسیدی آهن
آسیاب کردن سنگ آهن چگونه انجام می شود؟
آسیاب کردن پیش از انتقال ماده به مرحله جدایش ثقلی انجام میشود. در صورتی که آسیاب کردن مواد به خوبی صورت گرفته باشد، انتقال مجدد به مرحله سرند و خردایش به حداقل رسیده و انرژی کمتری در فرآیند فرآوری صرف خواهد شد. امروزه بیشتر در کارگاه های فرآوری سنگ آهن و در آسیاهای خود شکن و نیمه خودشکن به جای آسیاهای کلاسیک (میله ای – گلوله ای) انجام میشود.
در آسیاهای خودشکن سنگ های استخراجی پس از سنگ شکنی مرحله اول مستقیما وارد آسیای خودشکن شده و دانه های درشت ضمن آنکه خود خرد میشوند سایر ذرات را نیز خرد می کنند. در آسیای نیمه خود شکن قسمتی از بار مورد خردایش را گلوله های فولادی تشکیل میدهند. مقدار گلوله اضافه شده به آسیای نیمه خود شکن تا حدود 10 درصد حجم آسیا میرسد (در آسیای گلوله ای حجم واقعی گلوله ها حدود 20 تا 25 درصد حجم آسیا میباشد). در این آسیاها نسبت قطر به طول آسیا در حدود 3 میباشد. آسیا میتواند به صورت تر یا خشک کار کند. پس از خروج مواد از آسیاب، تقسیم بندی ذرات بزرگ و کوچک توسط سیکلون یا صفحه لرزان صورت میگیرد. به این ترتیب، ذرات بزرگ به مراحل قبلی و ذرات کوچک به مرحله بعدی منتقل میشوند.
جدایش ثقلی ذرات سنگ آهن
در جدایش ثقلی، ذرات سنگین سنگ آهن توسط نیروی گریز از مرکز از ذرات سبک جدا میشوند. این فرآیند به کمک مارپیچهای مخصوص و آب صورت میگیرد. در انتهای مارپیچهای جدایش ثقلی، مخزنی وجود دارد که مواد معدنی سنگین را در خود جمع کرده و مواد سبک را از درون فرآیند خارج میکند. به ماده معدنی جمع شده در مخزن مارپیچ، کنسانتره میگویند. با توجه به میزان جدایش مورد نیاز، این مرحله دو تا سه بار تکرار میشود.
همانطور که پیشتر ذکر کردیم اکثر مراحل عملیات ذکر شده به صورت تر انجام میگیرد و سنگ آهن پرعیار شده ی حاصل نیز حاوی آب میباشد و باید مرحله آبگیری و خشک کردن را بگذراند که در این مرحله رطوبت آن باید تا ۹ الی ۱۰ درصد کاهش پیدا کند. روند عملیات آبگیری و خشک کردن به این صورت است که سنگ آهن ها را روی فیلترهایی با ابعاد خاص قرار می دهند تا آب از آن ها جدا شود.
کنسانتره حاصله پس از عملیات آبگیری، سنگ آهن پرعیاری است که میتواند به انبار جهت دپو شدن منتقل گردد. همچنبن مواد اصطلاحاً باطله نیز که مواد غیر مطلوب در فرآیند محسوب می شوند، آبگیری شده و به تینکر منتقل میشود.
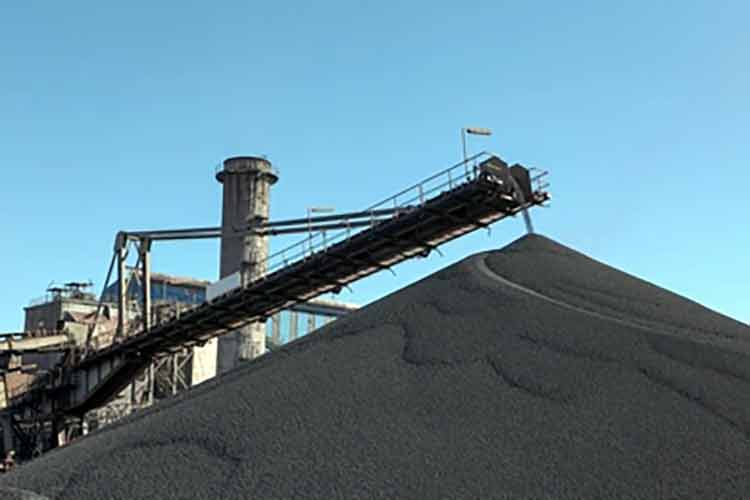
جدایش مغناطیس سنگ آهن
کنسانتره به دست آمده از خردایش و جدایش ثقلی از مقدار کمی سنگ آهن تشکیل شده است. به منظور افزایش عیار سنگ آهن، مواد جمع شده در مرحله جدایش ثقلی به طور مستقیم به فرآیند جدایش مغناطیسی انتقال داده میشوند. از روشهای جدایش مغناطیسی برای مواد معدنی دارای خاصیت مغناطیسی استفاده میشود. در این روش با ایجاد یک میدان مغناطیسی و عبور ماده معدنی از این میدان، ذرات دارای خاصیت مغناطیسی جدا شده و کنسانتره ماده معدنی تولید میشود. جداکننده های مغناطیسی که در این بخش مورد استفاده قرار میگیرند، انواع مختلفی دارند که عبارتند از: جدا کننده با شدت پایین، جدا کننده با شدت متوسط، جدا کننده با شدت بالا، و جدا کننده با گرادیان بالا. طبلکهای مغناطیسی در این مرحله، مواد دارای خاصیت مغناطیسی را به خود جذب میکنند. مواد سبک جدا شده در مرحله قبلی نیز درون کوره پخته میشوند تا آهن موجود در آنها نیز جدا شود. در انتهای فرآیند فرآوری، آهن فرآوری شده یا اصطلاحا گندله سنگ آهن به دست میآید. به منظور تولید آهن خالص، گندله به کارخانه ذوب انتقال داده میشود.
برای بررسی قیمت و خرید سنگ آهن وارد لینک روبرو شوید – قیمت سنگ آهن