تقریباً تمام آهن مورد استفاده امروزه از معادن سنگ آهن سرچشمه میگیرد و سالانه میلیاردها تن از آنها استخراج میشود. استخراج سنگ آهن به ما این امکان را میدهد که از آهن برای ساخت فولاد ساختمانها، وسایلنقلیه، ابزارآلات و کاربردهای بیشمار دیگر استفاده کنیم. بدون استخراج سنگ آهن دنیای مدرن پیش نمیرود.
استخراج سنگ آهن شامل فرآیند پیچیده و چند مرحلهای میشود. برای استخراج و فرآوری سنگ آهن برای مصارف صنعتی به ماشینآلات سنگین، فرآیندهای فنی پیشرفته و زیرساختهای گسترده نیاز است.
در این مقاله، نحوه بهدست آوردن آهن قابل استفاده از ذخایر سنگ خام را بررسی خواهیم کرد. شما در مورد روشهای مختلف استخراج و پردازش، اثرات زیستمحیطی و روشهای افزایش کارایی فرآوری سنگ آهن نکاتی را یاد خواهید گرفت.
مروری بر فرآیند استخراج سنگ آهن
استخراج سنگآهن به فرآیندهای معدنی که برای دسترسی داشتن و خارج کردن سنگها و مواد معدنی غنی از آهن از زمین اطلاق میشود. عمدهترین مواد معدنی حاوی آهن شامل هماتیت، مگنتیت، لیمونیت و سیدریت است. این سنگهای آهن بهصورت رسوبی، دگرگونی یا آذرین شکل گرفتهاند و روشهای استخراج بستگی به شرایط و محل ذخیره سنگ معدن دارد.
بهطور کلی، استخراج سنگ آهن شامل چندین مرحله عمده است. ابتدا، حفاری اکتشافی برای ارزیابی اندازه، مکان و کیفیت ذخایر سنگآهن انجام میشود. در مرحله بعد، تجهیزات سنگآهن را استخراج میکنند. پس از آن خرد کردن، غربالگری و تغلیظ سنگ معدن برای جداسازی آهن قابل استفاده از مواد زائد انجام میشود. در نهایت، پودرهای آهن فرآوری شده برای استفاده در تولید فولاد به کارخانههای فولاد منتقل میشوند.
کاربردهای اصلی سنگ آهن
اکثریت قریب به اتفاق سنگ آهنی که استخراج میشود برای تولید فولاد استفاده میشود. در واقع سنگآهن حدود 95 درصد از کل فلز مورد استفاده در تولید فولاد را تشکیل میدهد. محتوای آهن بههمراه مواد اولیه دیگر برای فولادسازی آماده میشوند و از طریق پالایش و آلیاژسازی آنها به فولادهای متنوع با خواص فیزیکی مختلف بر اساس نیاز کاربری تبدیل میشوند.
در کنار فولاد، از سنگ آهن در سایر کاربردهای مهم استفاده میشود، بهعنوان مثال، میتوان سنگ آهن را به رنگدانههای اکسید آهن مورد استفاده در رنگ، کاغذ، پلاستیک و سرامیک تبدیل کرد. همچنین از نانوذرات اکسید آهن برای کاتالیزورهای صنعتی استفاده میشود. آهن یک ماده مغذی ضروری برای انسانها و حیوانات است، مقداری از سنگ معدن استخراجشده به مکملهای آهن و کودهای گیاه افزوده میشود تا بدن موجودات و بافت گیاهها را تقویت کند.
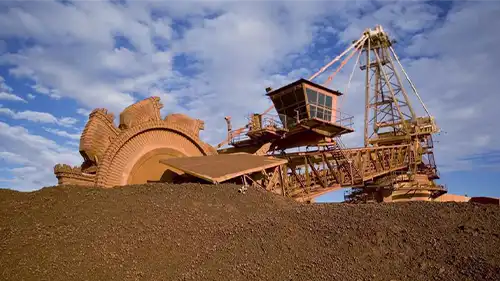
روشهای استخراج سنگ آهن
به طور کلی دو روش استخراج سنگ آهن وجود دارد، استخراج سطحی و استخراج زیرزمینی عمده نحوه بدست آوردن این سنگ معدنی را تشکیل میدهند. انتخاب یکی از این دو تکنیک به عواملی مانند مکان و خصوصیات زمین شناسی بستگی دارد.
برای مشاهده لیست قیمت سنگ آهن امروز روی این لینک کلیک کنید
روشهای استخراج سطحی سنگ آهن
استخراج سطحی به طور دقیق به دسترسی به ذخایر سنگ آهن نزدیک به سطح زمین اشاره دارد و زمانی انجام میشود که سنگ آهن باکیفیت بدون نیاز به حفاری عمیق در دسترس باشد. روش سطحی به دو شکل معادن روباز و نواری صورت میگیرد.
– تکنیک استخراج معدن روباز
استخراج روباز زمانی مناسب است که بدنههای سنگ معدن بزرگ بوده و نزدیک سطح زمین باشند. این تکنیک مستلزم حفر گودالهای روباز بزرگ در زمین برای آشکار کردن ذخایر سنگ معدن و حفاری آن است. این روش نسبت بالایی از ذخایر سنگ معدن را حاصل میکند. تخمین زده میشود که بیش از 95 درصد تولید سنگآهن از معادن روباز حاصل میشود و به نوعی محبوبترین روش استخراج سنگ آهن است.
– روشهای استخراج نواری
استخراج نواری مشابه استخراج روباز است اما شامل برداشتن مواد اضافی سطحی در نوارهای طولانی است. این روش زمانی استفاده میشود که ذخایر سنگآهن نسبتاً نازک باشد یا به مانند معادن روباز عمق کافی را نداشتهباشد. استخراج نواری سنگ معدن بهصورت افقی در اطراف تپهها و کوهها انجام میشود.
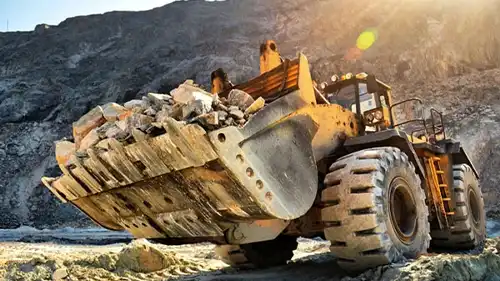
تکنیکهای استخراج زیرزمینی سنگ آهن
زمانی که ذخایر سنگ آهن بیش از حد در زیر سطح زمین قرار میگیرند، نیاز به استخراج زیرزمینی است. این روش نگرانیهای ایمنی بیشتر و هزینههای بالاتری در مقایسه با تکنیکهای روباز دارد. سه روش استخراجی اتاقی، ماینینگ و انفجاری از جمله روشهای استخراج زیرزمینی سنگ آهن است.
– استخراج اتاق و ستون
این روش شامل حفاری اتاقهایی با ستونهای نگهدارنده است که برای حمایت از سقف حفاری نمیشوند. اتاقها معمولاً تا هزار متر عرض دارند و ستونهای آنها هم میتوانند تا 100 متر ضخامت داشته باشند. با پیشرفت ساخت معدن، سنگ معدن قابل بازیافت بهترتیب از اتاقهای حفاری شده استخراج میشود و در آخر ستونها برداشته میشوند.
– ماینینگ دیوار طولانی
در این روش از قیچیهای خودکار برای برش بخشهای دیوار بلند سنگ معدن استفاده میشود. تکیه گاههای هیدرولیک بهطور موقت سقف را در حین کار برش نگه میدارند. با پیشرفت فرایند استخراج معدن، سقف بخش فرآوری شده فرو ریخته میشود تا مواد آن هم استخراج شود و بازدهی معدن افزایش یابد.
برای مشاهده لیست قیمت آهن اسفنجی امروز روی این لینک کلیک کنید
– انفجار ماینینگ
در این روش مواد منفجره برای شکستن رسوبات سنگ معدن استفاده میشوند، سپس از طریق تخلیه با استفاده از بالابر یا وسایلنقلیه، این مواد خارج میشوند. این روش محبوبیت بسیار کمتری دارد و مناسب ذخایر سنگ معدنی کوچک و شیبدار است. نگرانیهای ایمنی در مورد انفجار و تخلیه زیرزمینی در مورد این روش همیشه وجود دارد و باید با احتیاط انجام شود.
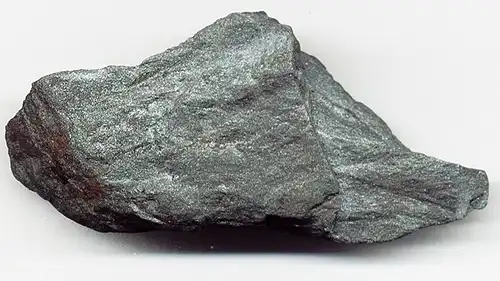
فرآوری سنگ آهن پس از استخراج
هنگامی که سنگ آهن با استفاده از تکنیکهای استخراج سطحی یا زیرزمینی استخراج شد، باید قبل از استفاده در تولید فولاد، فرآوری شود. فرآوری، سنگ معدن خام را به مواد غلیظ و با عیار بالا تبدیل میکند که برای ساخت فلزات و محصولات نهایی مناسب است.
– خرد کردن سنگآهن خام
سنگ آهن استخراج شده از معادن معمولاً اندازههای بزرگی – بیش از 1 متر مربع – دارند. ترکیب آنها هم به طور معمول غیریکنواخت است و محتوای آهن متفاوتی دارند. ابتدا باید سنگ معدن را بهاندازههای کوچکتر خرد کرد تا ذرات آهن برای جداسازی آزاد شوند. خرد کردن اولیه با استفاده از سنگ شکنهای فکی یا چرخشی انجام میشود. سپس خرد کردن ثانویه با استفاده از سنگ شکنهای مخروطی انجام میشود تا قطعات سنگ آهن به جستههای کوچکتر از پیش تبدیل شوند.
پس از خرد کردن، عمل غربالگری، تودههای سنگ معدن درشت را از مواد ریزتر جدا میکند. این فرآیند غربالگری سبب توزیع صحیح اندازه ذرات برای پردازشهای آتی میشود.
– سنگ زنی و غربالگری ریزه سنگآهن
دانههای ریزتر سنگآهن با اندازه کمتر از 1 میلیمتر، ریزدانه سنگآهن محسوب میشوند. آسیابهای مخصوص با گلولهها یا میلههای فلزی برای خرد کردن سنگ خرد شده به پودر بسیار ریز استفاده میشود. پس از آسیاب، ریزه سنگ معدن تحت غربالگری بیشتر گرفته و بر اساس اندازه ذرات طبقه بندی میشود. غربالگری مناسب، توزیع یکنواخت در واحدهای جداسازی را برای بازیابی بالاتر تضمین میکند و سبب جلوگیری از آسیاب بیش از حد و استهلاک مضر میشود.
– تغلیظ سنگآهن با جداسازی مغناطیسی
سنگ آهن از چندین اکسید آهن مختلف تشکیل شدهاست که دو نوع رایج آنها هماتیت (Fe2O3) و مگنتیت (Fe3O4) است. مرحله بعدی فرآوری سنگ آهن، جداسازی مغناطیسی برای تغلیظ محتوای آهن است. در جداسازی مغناطیسی، سنگ معدن خرد شده بر روی یک نوار نقاله با استفاده از یک میدان مغناطیسی قوی حرکت میکند.
خواص مغناطیسی اکسیدهای مختلف آهن متفاوت است، به همین امکان جداسازی از یک دیگر فراهم میشود. هماتیت از نظر مغناطیسی ضعیف است، بنابراین به راحتی مسیر را ترک کرده و از مابقی جدا میماند در حالی که مگنتیت بهشدت مغناطیسی است پس به نوار نقاله میچسبد.
جمعبندی
استخراج سنگ آهن یک فرآیند پیچیده و چند مرحلهای است که بر اساس نوع معدن متفاوت است. روشهای استخراج سطحی مانند استخراج معادن روباز و نواری ترجیحاً برای ذخایر بزرگ یا کم عمق آهن استفاده میشوند، در حالی که تکنیکهای زیرزمینی مانند استخراج اتاقی، امکان دسترسی به سنگ معدنهای عمیق را فراهم میکنند. صرفنظر از روش استخراج، سنگ آهن خام خارج شده نیاز به پردازش گستردهای از جمله خرد کردن، غربالگری، آسیاب و جداسازی مغناطیسی دارد.
برای مشاهده لیست قیمت سنگ آهن امروز روی این لینک کلیک کنید