مقالات مرتبط
پروسه ریخته گری و فرآوری چدن و فولاد
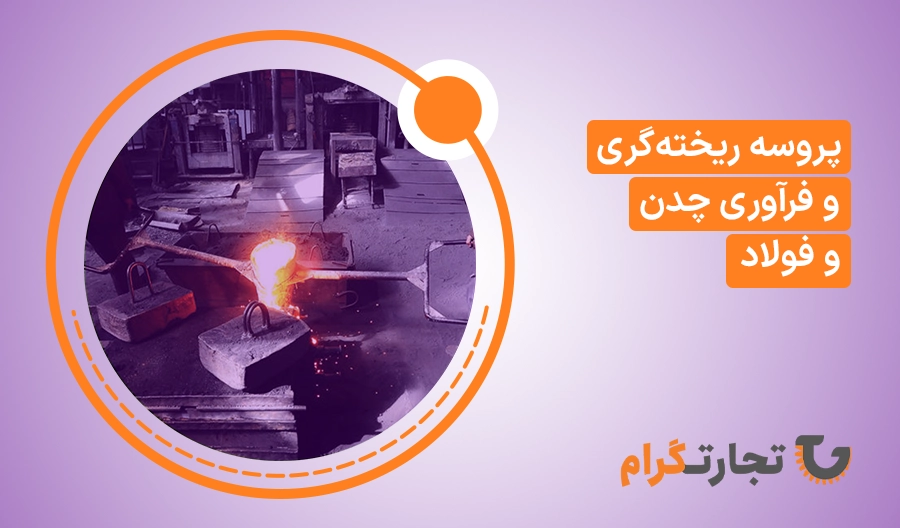
از تولید قطعات درونی لباسشویی و انواع لوازم خانگی و ساختمانی گرفته، تا قطعاتی که در سیستمهای پمپاژ و بخار در صنعت دریانوردی، مورد استفاده قرار میگیرند، همگی جزو قطعات تولیدی از ریختهگری چدن و فولاد هستند. پروسه ریختهگری و فرآوری چدن و فولاد، شامل مراحل پیچیده و روشهای متعددی است که آلیاژهای آهن را که حالت شکننده دارند را نرم میکنند و برای ساخت انواع قطعات به کار میبرند. در ادامه مطلب قصد داریم علاوه بر بررسی کامل مراحل ریختهگرس فولاد و چدن آهن، کاربردها و انواع روشهای انجام این فرآیند را ذکر کنیم. چنانچه قصد کسب اطلاعات در این زمینه را دارید، با ما همراه باشید.
مراحل ریخته گری چدن و فولاد چگونه است؟
فولاد و چدن هر دو فلزی آهنی هستند و معمولاً از ماده اولیه یعنی خاکستر آهن و آهن خالص تولید میشوند. تفاوت اصلی این دو فلز، در میزان کربن آنها است که فولاد میزان کربن کمتری نسبت به چدن دارد؛ اما فرایند ریختهگری آنها به یکدیگر شبیه است و به طور کلی پروسه ریختهگری و فرآوری چدن و فولاد، طبق مراحل زیر انجام میشود.
آماده سازی الکترودها
برای ریختهگری و ذوب فلزاتی همچون فولاد و چدن، ابتدا باید الکترودهای مورد استفاده در کورهها، آماده باشند. آماده سازی الکترودها در کورههای القایی و به منظور ایجاد قوس الکتریکی و ذوب فلزات انجام میشود.
ذوب مواد به همراه افزودنیهای آن
در مرحله دوم، مواد اولیه که شامل فلزات آهنی مانند چدن و فولاد هستند را به همراه مواد افزودنی، مانند نیکل، کروم و کربن را به کورهها، برای ذوب شدن اضافه میکنند.
تصفیه
در این مرحله برای اینکه خواص فلزات را بهبود ببخشند، آلایندهها و مواد اضافی را حذف میکنند. مرحله تصفیه، توسط یک سری فرایندها و روشهایی همچون خردایش، غربالگری، شستشو و تمیز کردن مادهها انجام میشود. در واقع در این مرحله، خاک و سنگهای غیر معدنی و اضافی را برای مرحله قالب گیری، از ماده اصلی حذف میکنند.
قالب گیری
بعد از اینکه تمامی مواد ذوب شدند و مواد غیر ضروری تصفیه شدند؛ حالا نوبت به مرحله قالبگیری است. در این مرحله از قالبهای دائم و موقت استفاده میشود که این قالبها در جنسهای مختلفی مانند شن، ماسه، فولاد و دیگر مواد هستند. نوع طراحی، اندازه و شکل قالبها، متناسب با نوع قطعه مورد نیاز انتخاب میشود.
خنک سازی و تثبیت
در این مرحله، قطعات فولاد و چدن را که به صورت مذاب داخل قالبها ریخته شدهاند را ابتدا خنک میکنند؛ سپس آرام آرام به حالت جامد تبدیل میکنند. مرحله خنک سازی و تثبیت، با استفاده از روشهایی همچون، خنک سازی با هوا، خنک سازی با آب و خنکسازی با روغن و دیگر روشها، انجام میشوند. هدف اصلی از این مرحله، علاوه بر جامد شدن این مواد، بهبود خواص فیزیکی و تثبیت ساختار فلزات و شکل آنها است.
پس پردازش
گاهی اوقات پس از خنک کاری و تثبیت، نیاز به عملیاتی همچون تمیزکاری، برش، حرارت دهی، تغییر شکل و دیگر عملیاتها است. این فرآیندها را با استفاده از تکنیکهایی همچون نیتریداسیون و ماشین کاری و به منظور بهبود کیفیت و خواص فیزیکی آن محصول، انجام میدهند.
مراحل نام برده، همگی مراحل ریخته گری چدن و فولاد هستند. که ریختهگری فولاد و چدن، روشهای متعددی دارد که در ادامه به بررسی این روشها میپردازیم.
انواع روشهای ریخته گری فولاد و چدن کدامند؟
روشهای ریختهگری چدن و فولاد شامل موارد زیر هستند.
● ریخته گری به روش شناور
در این روش، فلزهای چدن و فولاد را در قالبهای شناور که در جنسهای مختلفی همچون سیمان، سنگ، شن، ماسه و گچ هستند، میریزند؛ سپس این قالب را درون یک محیط مایع که تحت تاثیر نیروی گرانشی قرار دارد، میگذارند و این مواد مذاب، به آرامی خنک میشوند و سپس به شکل جامد در میآیند.
●ریخته گری به روش فشاری
در روش ریخته گری با فشار، فولاد یا چدن مذاب را به وسیله فشار در داخل قالبها جای میدهند. قالبهای به کار رفته در این روش، معمولاً از جنس فولاد و آلومینیوم هستند. در مرحله بعدی، قطعه ریخته شده از قالب را خارج میکنند. با استفاده از این فشار نه تنها نیروی جاذبه را کاهش میدهند؛ بلکه خواص مکانیکی قطعه بهبود پیدا میکند. همچنین به دلیل مقاومت بالای قطعات تولید شده این روش، از محصولات تولیدی آن در ساخت قطعات خودروسازی، هوافضا، صنعت نفت و گاز و صنایع ساختمانی و دیگر صنایع استفاده میشود.
●ریخته گری به روش مومی (investment casting)
در این روش، ابتدا قالب مومی را که به صورت یکبار مصرف برای هر مرحله از ریختهگری است، را از موادی همچون موم و پلاستیک پر میکنند؛ سپس قالب را از الگو جدا میکنند. بعد از اینکه موم، پلاستیک فولاد یا چدن مذاب شدن، به طور مستقیم به داخل قالب اصلی ریخته میشوند. بعد از اینکه مواد مذاب خشک شدند؛ حالا قالب موقت به شکل قطعی و نهایی در میآید و آن را جدا میکنند.
●ریخته گری به روش مداوم
در ریختهگری به روش پیوسته (مداوم)، تمام فرایندهای ریختهگری تا شکل گیری نهایی، به صورت پیوسته و درون یک دستگاه انجام میشود. در این روش، مواد مذاب در هر مرحله از دستگاه جدا نمیشوند. فولاد و چدن را با استفاده از یک قالب (تاندیش) به صورت مستقیم و به صورت مداوم در قالب ریخته میریزند؛ سپس این قالب، به آرامی از درون دستگاه عبور میکند و طی دو مرحله سرمایش ثانویه و نهایی به شکل قطعه مورد نظر تبدیل میشود.
علاوه بر روشهای ذکر شده، روشهای دیگری مانند ریختهگری القایی، سریع، فرسابی، دیزاماتیک و دیگر روشها، برای ریختهگری چدن و فولاد وجود دارند که روشهای ذکر شده، بیشترین کاربرد را دارند. چدن، دارای انواع گوناگونی است که در ریختهگری عموما از چدن داکتیل و چدن خاکستری استفاده میشود. در ادامه به بررسی نحوه ریختهگری این نوع چدنها با استفاده از روشهای اختصاصی آنها میپردازیم.
روشهای منحصر به فرد ریختهگری چدن و فولاد
از جمله روشهای منحصر به فرد ریختهگری چدن و فولاد میتوان به موارد زیر اشاره کرد.
●ریختهگری چدن نشکن یا داکتیل
منیزیم و سدیم، ماده اصلی مورد استفاده در این روش هستند. این مواد، به مواد مذاب چدن اضافه میشوند که منیزیمهای اضافه شده، توانایی تغییر ساختار چدن را دارند؛ از این رو، چدنها را به راحتی میشکنند و فرم دهی وشکل گیری چدنها، راحتتر میشود. به دلیل اینکه ساختار شکنندگی چدنها در این روش از بین میرود، کاربرد و استفاده از داکتیلهای چدن بیشتر میشود.
● ریختهگری ماسه Co2 حساس
همانطور که گفتیم چدن، از سه عنصر آهن، کربن و سیلیسیم تشکیل میشود. برای ساخت قطعات فلزی فرم دار، باید از ریختهگری چدن استفاده کنیم که برای این کار، میتوان از ماسه استفاده کرد؛ چرا که دمای ذوب چدن، بیشتر از دمای ذوب آهن است. در گذشته از ماسههایی کنار دریا و ته رودها، برای پروسه ریختهگری چدن و فولاد استفاده میکردند. امروزه با پیشرفت علم و تکنولوژی، از ماسههای Co2 حساس استفاده میشود. ماده اصلی ماسههای Co2 حساس، چسب سیلیکات است. در اثر ترکیب این چسب با ماسههای سیلیسی و گاز Co2، یک قالب بسیار مقاوم و محکم برای فرایندهای ریختهگری به دست میآید. ناگفته نماند در این روش نه تنها دقت فرآیند ریختهگری بالاتر میرود، تراشکاری قطعات چدنی هم کمتر میشود.
● ریختهگری ماهیچه محافظ
منظور از ماهیچه محافظ در ریختهگری چدن، یک جز کاملا جداگانه است که در قطعاتی که برای محفظه اصلی، به فضای خالی نیاز دارند، به کار برده میشوند. از ماهیچههای محافظ در مواقعی که زائدههای خارجی، هم سطح نیستند، به عنوان قطعات آزاد نیز استفاده میشود.
در مطالب فوق به بررسی روشهای منحصر به فرد ریختهگری چدن پرداختیم که قطعات تولیدی از هر کدام از این روشها، با توجه به کیفیت، مقاومت و شکل نهایی که دارند، در صنایع مختلف به کار میروند. در ادامه به بررسی مهمترین کاربردهای قطعات تولید شده در طی پروسه ریختهگری و فرآوری چدن پ فولاد میپردازیم.
کاربرد قطعات تولیدی در ریختهگری چدن و فولاد چیست؟
کاربردها و موارد استفاده از محصولات فرآوری چدن و فولاد، در صنایع مختلف، کاربرد دارد که در ادامه به برخی از این کاربردها و محصولات تولیدی اشاره میکنیم.
صنعت خودروسازی
یکی از ویژگیهای اصلی محصولات تولید شده در ریختهگری چدن و فولاد، مقاومت بالای آنها در برابر عوامل فرسایش است؛ از این رو در صنعت خودروسازی برای ساخت بلوک موتور، سرسیلندر، پیستون، کاتر، سیستم تعلیق ترمز و دیگر قسمتهای مربوط به خودرو مورد استفاده قرار میگیرند.
صنعت ساختمانی
محصولات تولیدی طی پروسه ریختهگری چدن و فولاد، دارای مقاومت و تحمل بالایی در برابر وزنهای سنگین هستند؛ از این رو در صنعت ساختمانسازی، برای ساخت سازههای فلزی برای تثبیت سازهها ، بالابرها، پلهها، دربها، ستونها و دیگر محصولات از آنها استفاده میشود.
صنعت نفت و گاز
تحمل در برابر فشار، یکی دیگر از ویژگیهای محصولات فرآوری پس از ریخته گری فولاد و چدن است. در تهیه انواع لولهها، شیرها، فلنجها، صفحات مبدل حرارت و قطعاتی که در استخراج نفت و گاز استفاده میشوند، از این محصولات استفاده میشود.
علاوه بر کاربردهای ذکر شده، در صنعت لوازم خانگی و برای ساخت انواع قطعات لباسشویی و لوازم برقی و همچنین در صنعت کشاورزی در تهیه انواع ماشین آلات و تجهیزات کشاورزی نیز، این محصولات کاربرد دارند که کیفیت این محصولات تولیدی، تاثیر فراوانی بر عملکرد آنها دارد.
سخن پایانی
پروسه ریخته گری و فرآوری چدن و فولاد با استفاده از روشهای متعدد و توسط دستگاهها و تجهیزات فراوانی، انجام میشود. از قطعات تولیدی پس از ریخته گری فولاد و چدن، در صنایع مختلفی از این محصولات استفاده میشود در واقع کیفیت مواد ریختهگری و همچنین تجهیزات و دستگاههایی که در این پروسه به کار گرفته میشوند عامل مهمی در کیفیت نهایی محصولات و قطعات تولیدی دارند.
دیدگاه خود را بنویسید
مقالات مرتبط